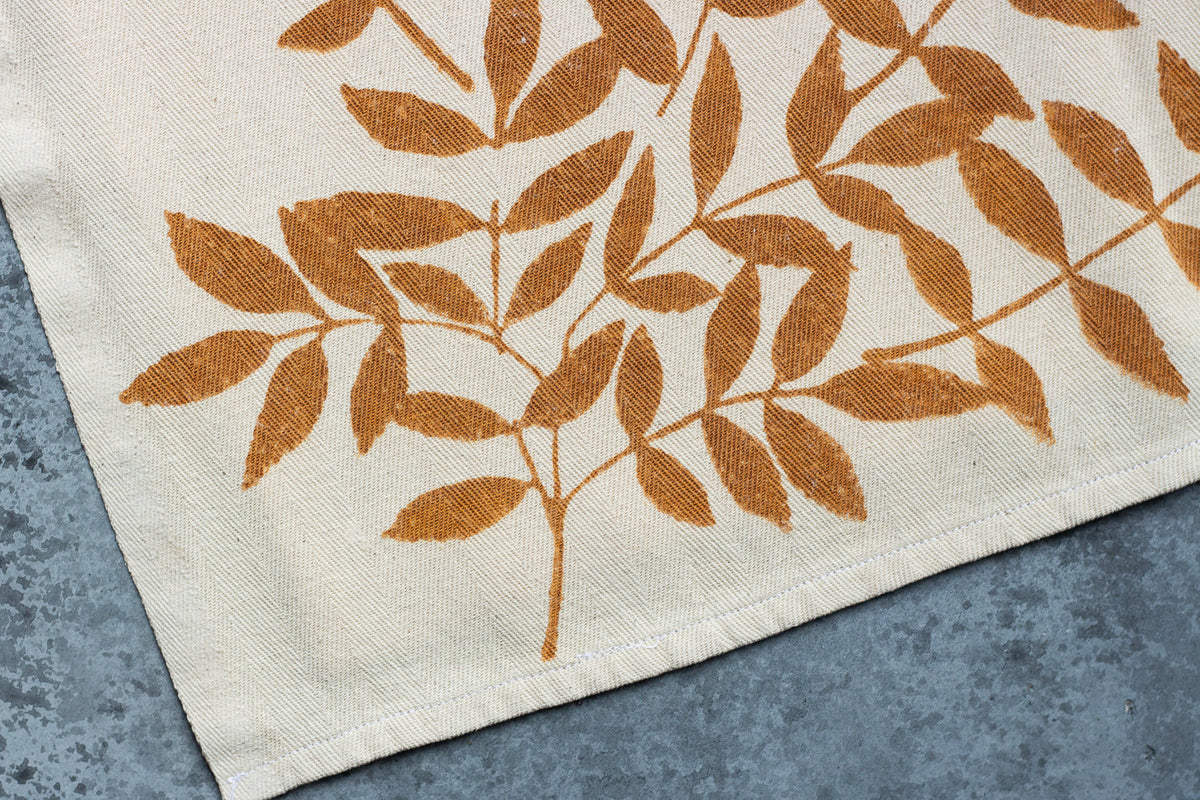
The Art of Rust Printing
|
|
Time to read 4 min
|
|
Time to read 4 min
There’s something to be said for the effortless countryside aesthetic found in many Italian kitchens – a look that so many of us try to capture at home (and can you blame us?). As with most things, the devil is in the details: a chipped porcelain pitcher adorned with bright florals, casually mismatched tumblers, and a never-ending flow of nameless local wine. And, inevitably, billowing tablecloths and napkins that have seen hundreds of convivial dinners just like this one before it.
Step inside any home or trattoria in Emilia-Romagna, and you’ll likely find just such rustic details blending seamlessly into the background – the “je ne sais quois” of Italian decor – including an array of linens boasting rich ochre, pomegranate red, or emerald green patterns that evoke the surrounding landscape itself. Here, these details are not just for show, to capture some wanderlust-invoked memory of sunflower fields and plates of tagliatelle alla bolognese. The unique craft of hand-dyed textiles dates back centuries and is carried on today by a group of artisans who don’t just honor the tradition but have also made their own mark on the art form.
Typical to Romagna (the stretch of the region that goes roughly from Ravenna down to Rimini, hugging the Adriatic coast), this method of textile printing calls for hand-carved stamps made from soft pearwood, all-natural dye created from rust and vinegar, and simple materials like cotton, linen, and hemp (the most traditional, and most precious) that have been produced in the area for centuries.
This method of hand-printing was common in Europe from the 1400s to the 1700s. But even as new technologies emerged for textile printing, the artisans of Romagna carefully preserved and passed down their craft through the generations.
Typically, the hand-carved molds used to create the textile patterns reflect their place of origin: grapevines, roosters, flora, and fauna, although some are far more ornate. Each stamperia, or printing studio, boasts their own repertoire of patterns – which become the artists’ calling card.
The process requires just four simple tools: hand-carved wooden molds, a mallet, dye, and cloth. Today’s artisans still follow the same basic and time-honored process: the fabric (usually linen, hemp, or cotton) is laid flat on the worktable, the stamp is placed dye-side down onto the fabric, and the artist quickly, evenly, and rhythmically taps the stamp with a heavy mallet to evenly distribute the color, which gently seeps into the fabric.
Of course, it’s all much easier said than done. The artisans must acquire a careful, even hand when applying the dye to the stamps – too much, and it will bleed through; too little, and the result will be too faint. The final weight of the pattern is a mark of the artisan’s even hand.
And the dye? This, too, remains a Romagnolo secret. In fact, each stampatore holds his or her own recipe for their dyes close, as any painter might not reveal their personal techniques for blending color. The base, however, is more or less the same: iron rust, vinegar, and starch, combined to make an all-natural paste with a greyish tint.
Once dyed, the linens are laid out to dry, then washed the day after in a caustic solution to rinse out excess dye and set the color. And here is where the magic happens: upon coming into contact with the rinse, the pattern’s grey hue emerges as a brilliant copper.
Imitation may be a form of flattery, but certainly not when it comes to artisan craftsmanship. It’s common to find cheap imitations, given the time-consuming, expensive, and labor-intensive nature of the craft. In fact, the top artisans of the region have since created an Association of Romagnolo Printers, instated to protect the art form and promote the authenticity of their products (any rust-printed textile you find here at q.b. is a member of this association). When looking for authentic rust-printed textiles, there are a few telltale signs of an original handmade piece.
First, flip the textile over and you’ll notice that the pattern and color are completely visible even from the back. You might even notice slight irregularities in the pattern – this is a good thing! It’s a sure sign that the pattern was stamped by hand. Next, examine the pattern again from the front. If you notice slight imperfections in the pattern, this is again a good sign. Since each mold is placed by hand to achieve a repeat pattern, the lines might show some slight imperfections.
Finally, there will naturally be some bleeding of the dye. Unlike silk-screen printing, which results in a flat and uniform color distribution, each block of the rust-dyed pattern is applied by hand, and this can make for slight irregularities in the color. (Think about taking a rubber stamp to a sheet of paper: even if you reapply the dye every time, maybe you apply less pressure one time, more the next…in the end, no two stamps turn out exactly the same.)
The beauty of these all-natural linens is that they are sturdy and durable as anything, meant to be used and enjoyed every day (just as any Italian would). For the first wash, be sure to wash your linens on their own on a warm, non-soak cycle with a neutral soap (we go for Marseille) and – trust us on this – a splash of bleach added to the fabric softener tray. The bleach will actually set and brighten the color of the textiles.
After this first “treatment,” you can wash the linens on warm (up to 122°F) with neutral detergent, using the above bleach method as needed to remove any stubborn stains.
However, take note: you never want to use stain removers, additives, or fabric softeners on these products. Chemicals like hydrogen peroxide can discolor the natural dye (and even wear holes into the fabric over time).
Remember: each hand-dyed textile is completely unique. When you invest in one of these textiles, you’re investing in the preservation of a centuries-old craft that only a handful of artisans still practice today. Now if that doesn’t make your home a little more Italian, we’re not sure what will.